warrenpenalver
Active member
I have decided that i want to see how crazy i can go and design a carbon chassis.
It will be based dimensionally around the wheelbase and rough dimensions of the puma but the body panels themselves will in essence be cosmetic/weatherproofing only.
This is not going to be a quick project so if youre hoping to see a carbon chassis built in the next few months then look elsewhere
Initially its a design exercise, mostly in solidworks CAD along with some destructive testing of representative test panels etc to refine the design and structural strength as required.
Hopefully if it works out feasable then i will build the chassis and as a full car. I already own over 100 square meters of carbon, most of the core material i need. The rest i can source through work at cost price so in terms of affordability, a simple monococque chassis isnt as expensive as you might think in material costs.
Firstly i need to re-learn CAD. Its all changed since i did it back in 1999/2000 and moved from being programmed by hand to being based on mouse commands and a simple menu interface. Should be able to learn it fairly quickly and much quicker than it took me to learn C and program in linux k-shell.........
A few fixed constraints,
Must fit within puma profile
same wheelbase as current puma.
Will be engineered for cossie drivetrain
ability to add steel roll cage if full roof and roll over protection not already built into design.
Im still in split minds about using cossie based suspension set up or going the full hog and designing a double wishbone set up front and rear. Have some suspension design reading to do over the next few months and a fair few calculations to work out what is the best way forward.
Few initial rough sketches based on cossie subframes and beam:
Will be a lot of work to get anywhere near a functioning design but will get there eventually.
It will be based dimensionally around the wheelbase and rough dimensions of the puma but the body panels themselves will in essence be cosmetic/weatherproofing only.
This is not going to be a quick project so if youre hoping to see a carbon chassis built in the next few months then look elsewhere
Initially its a design exercise, mostly in solidworks CAD along with some destructive testing of representative test panels etc to refine the design and structural strength as required.
Hopefully if it works out feasable then i will build the chassis and as a full car. I already own over 100 square meters of carbon, most of the core material i need. The rest i can source through work at cost price so in terms of affordability, a simple monococque chassis isnt as expensive as you might think in material costs.
Firstly i need to re-learn CAD. Its all changed since i did it back in 1999/2000 and moved from being programmed by hand to being based on mouse commands and a simple menu interface. Should be able to learn it fairly quickly and much quicker than it took me to learn C and program in linux k-shell.........
A few fixed constraints,
Must fit within puma profile
same wheelbase as current puma.
Will be engineered for cossie drivetrain
ability to add steel roll cage if full roof and roll over protection not already built into design.
Im still in split minds about using cossie based suspension set up or going the full hog and designing a double wishbone set up front and rear. Have some suspension design reading to do over the next few months and a fair few calculations to work out what is the best way forward.
Few initial rough sketches based on cossie subframes and beam:
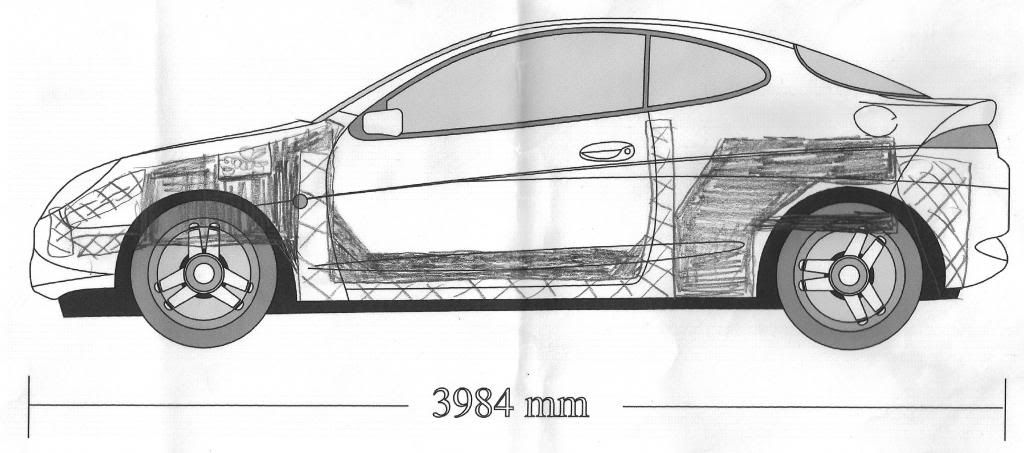
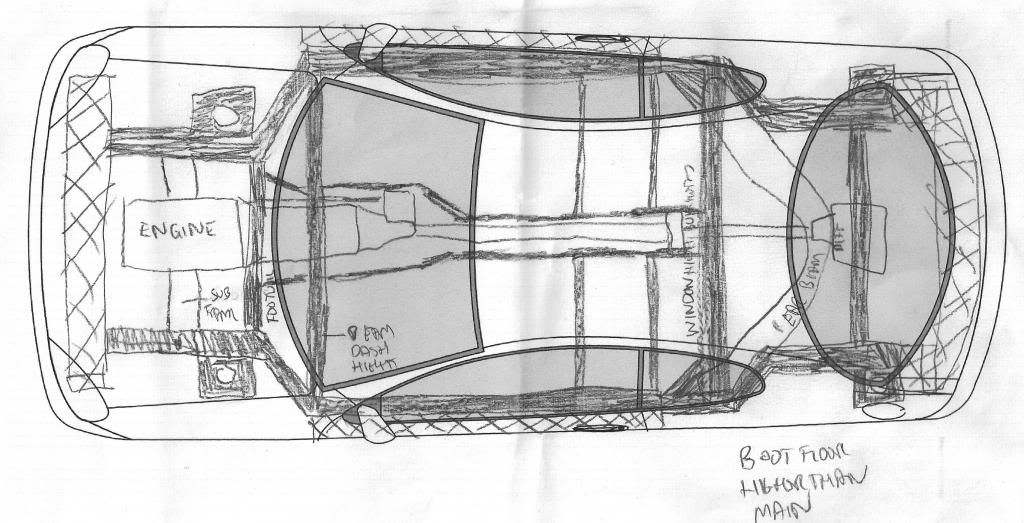
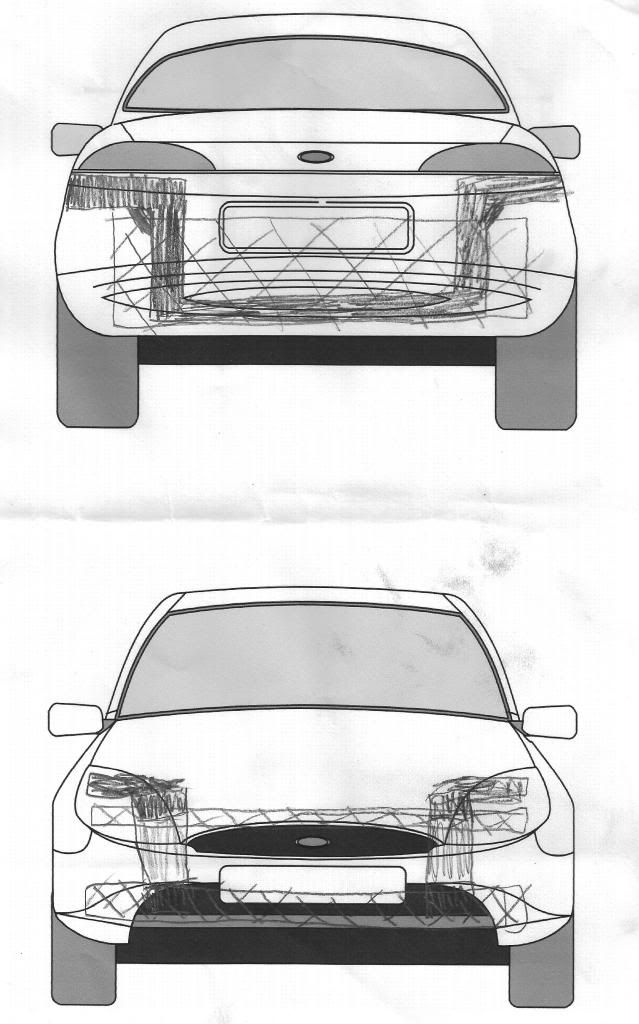
Will be a lot of work to get anywhere near a functioning design but will get there eventually.